Flooring Answers: Q&A
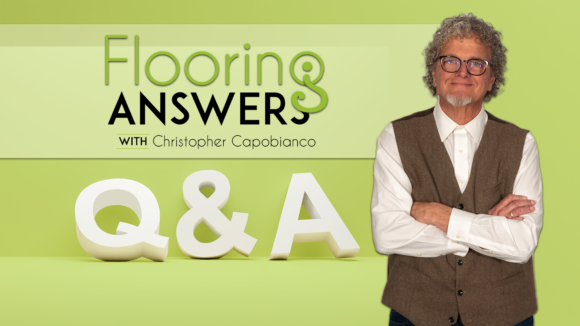
From California to Massachusetts to Florida, we asked Spartan reps to list out some of their frequently asked questions from clients. From those questions, we give you Flooring Answers: Q&A! Check out the nitty gritty below as FA columnist Christopher Capobianco tackles each question with every detail you’ll ever need.
Q: Vinyl tile/plank is getting popular in thicker versions like 5mm as opposed to the traditional 3mm or 2.5mm. I don’t mean the “click” floating floor products but the category of 5mm products sold as “loose lay.” Many of them require “glue down” installation in commercial applications. This is confusing – can you explain?
I understand this confusion, but some manufacturers have changed their “sales pitch” so “Loose Lay” is not mentioned as prominently.
First, it’s important to note that these products ALWAYS require adhesive. “Loose lay”means that adhesive is applied around the perimeter, and the rest of the floor is installed without adhesive. So “loose lay” does not mean “no adhesive.” The other option is a fully adhered installation, the preferred method for commercial spaces.
My own experience with 5mm vinyl tile and plank has always been fully adhered for commercial applications. So, why spend more for the thicker material if its glued down anyway? Designers like the fact that the 5mm thickness transitions nicely to carpet tile, so transition moldings are often not needed. Flooring contractors have told me that the extra thickness makes a noticeable difference in minimizing telegraphing of minor substrate irregularities. For example, I worked on a 5mm plank installation in a small office building that allowed the installer to go over an old asbestos containing sheet vinyl without the need for abatement (see image on the left).
So, in a nutshell – the “loose lay” (perimeter-adhered) method is typically used for residential, temporary, or raised access floor applications, and a fully adhered method is best for all commercial applications. Hopefully, as this category evolves, the manufactures that have not modified their literature will do so to eliminate this confusion.
Q: Please explain the difference between a LVT “wear layer” and a PVC Free product that has a “wear surface”.
“LVT” is a not a flooring category but is a marketing term applied to printed vinyl tile and plank. Many (but not all) of these products meet the requirements of ASTM F1700, Standard Specification for Solid Vinyl Floor Tile, Class III Printed Film Vinyl Tile. In these products, a separate layer of transparent or translucent vinyl is applied over the print layer. Today, many products are also made with an additional layer of UV-cured polyurethane for added protection. Per F1700, “for commercial applications, the wear layer shall be a minimum of 0.020 inches (0.5 millimeter) thick. This is also referred to as “20 mils.”
“PVC Free” versions of these products look similar but are manufactured with different processes and ingredients. Rather than clear vinyl, these tile and sheet products may use factory applied polyurethane (PU) as the surface wear layer. These coatings are more durable than vinyl, and are often a part of the printed layer, as opposed to a separate layer on top of the print. As such, a thickness measurement comparison to vinyl may not be possible. However, these products have been proven to be very durable and stain resistant in actual applications and compare favorably to vinyl products. Evaluations have shown that at times 5 to 7 mils of urethane is equivalent to 20 mils of clear PVC when abrasion comparison testing is conducted per the ASTM D 3884 Tabor Abrasion test.
Q: With so much discussion of acoustics for residential and hospitality applications, I am seeing terms like IIC, STC, and NRC. What does it all mean – and do they all apply to floors?
During the last few decades, there’s been a shift from carpet in residential buildings, hotels and offices. The unintended result of this is a situation I call“one man’s ceiling is another man’s floor.” That’s the title of a great Paul Simon song from 1973, but it also refers to impact noise from walking and other activities that pass through a floor and into the space below it. This condition was not noticed when floors were carpet. Now that hard surfaces are being used, it can be a source of stress between neighbors. As a result, noise reducing flooring systems have been developed. That’s why there’s a rise in acoustic underlayment or attached cushion beneath wood, tile or vinyl. At the same time, test methods and ratings have been developed for various acoustic characteristics.
Ratings & Classifications
- First, IIC and STC numbers are not measurements from test methods – they are ratings from classifications that interpret test method measurements.
- IIC (Impact Insulation Class) ratings reference structure-borne sound, meaning sound that transmits through the floor/ceiling assembly by direct contact. Examples of this are dragged furniture, dropped objects, jumping or foot/paw steps.
- STC (Sound Transmission Class) ratings reference airborne sound, meaning sound that transmits through floor/ceiling assemblies by air pressure. Examples of this are speech, TVs, musical instruments, and stereos. STC is not just used for walls – the classification specifically mentions floors in the scope. It’s tested in the exact same chamber as IIC and is becoming increasingly important to hospitality customers.
- NRC is “Noise Reduction Coefficient” that measures the sound within a space – specifically how much a particular surface absorbs sound. This is often a source of confusion when it comes to floors. I’ve often had this discussion about floors in areas like an office or conference room where the owner wants to reduce “echo” in the room. Resilient floors like cork or rubber have great reputations for excellent acoustic characteristics, but that’s more about sound transmission (IIC and STC). These are still smooth surfaces, so sound bounces off. As such, NRC numbers for these flooring materials are not good, so a floor like carpet would be preferred, or the sound can be absorbed by wall coverings or acoustic ceiling panels.
Q: For Glue down vinyl tile/plank applications with lots of glass which equals lots of sun which equals a lot of expansion and contraction… what type of adhesive should be used? I think every supplier should have a “disclaimer” for similar applications.
I agree this is an important point; I’ve seen complaints over the years for gapping vinyl tile or plank, and often temperature is a cause. My immediate answer would be to use two-part epoxy adhesives because they are hard-setting and have good resistance to extremes of temperature. However, does it say that anywhere? I checked five installation guides from five different manufacturers to look for this answer.
There are plenty of warnings about product acclimation and temperature conditions, such as storage of “material [and]adhesives in the acclimatized job site between 65°-85°F and 35%- 65% RH for 48-72 hours prior, all times during, and maintain temperature continuously after installation. However, as far as specific recommendations for floors exposed to sun, it’s rarely mentioned. One specification warned against sunlight during the installation process, saying “During Installation, direct sunlight should be blocked using window treatments or other protection.” Another warned against using in direct sunlight at all, saying “Do not install outdoors or in areas that may be exposed to repeated and sustained UV/IR rays, as product may fade, discolor or experience excessive movement.” As far as adhesive recommendations, I only found one mention: “For areas with…… direct sunlight, only use one-part reactive Modified Silane or two-part epoxy adhesive.”
In conclusion, it’s always important to ask questions about the project before the specifications are written, and material gets ordered. Direct sunlight, wet areas, rolling loads and other extremes may call for a different adhesive or even a different product altogether.
Q: In what settings do you decide which resilient flooring adhesive is used and why? For example, a hard setting adhesive goes in a hospital so that furniture can go on top, and the adhesive will not displace under the weight. What is used in multifamily and why? What about a gym setting and why? A bathroom and why?
In short, many adhesives are product specific and in other cases, the use of the space will dictate. Here are some examples.
Rubber floors, “PVC Free” materials and others require adhesive that’s specific to that material, usually a hard setting wet set type. A vinyl adhesive may work initially, but often will fail later.
For vinyl floors, remember there are different products and different adhesives. VCT adhesive is not the same one you’d use for “LVT”, and homogeneous solid vinyl requires a different one again. Sheet vinyl may be the same type of adhesive but a different methodology as far as the trowel size and open time.
Sometimes there are multiple adhesive recommendations for the same flooring product because different substrates and traffic areas have different requirements. For LVT in that Multifamily setting, the residential units would be light traffic (pressure sensitive adhesive) and the lobby would be heavy traffic that might require a hard-setting adhesive. For a bathroom or other area where the floor might get wet, a waterproof adhesive like urethane or epoxy would be preferred.
With so many different products and adhesives in the resilient flooring category, this could be an entire Flooring Answers column. I’ll return to this subject in the future.
Q: Which tile products have the appropriate coefficient of friction (COF) so there is good slip resistance for wet areas, like a spa? Are any of those products factory made this way, instead of adding another coating?
It’s true, products are made with different surface textures that can affect slip resistance, but tile size is also matters. Here are some points to consider:
- Polished finishes have a lower COF that Matte or textured finishes, so avoid them for wet areas.
- Mosaics are a good option for wet areas, even showers! Why? The smaller tile size equals more grout which means more places for water to go. Less water on the surface makes for a safer floor.
- Some products have a surface texture that’s inherently slip resistant. For example, quarry tile is used in commercial kitchens. Tile with textured finished (often called “grip” or “traction” finish) greatly improve COF and are slip resistant enough to be used in wet areas.
Thanks for reading!
I’d like to thank my Spartan colleagues for their great questions. Thanks also to John – Kahrs/Upofloor, Keith – Cobalt and Graham – AVA for helping with the some of the details.
Stay tuned our next Flooring Answers Q&A – Questions received by Customer Service.
DO YOU HAVE QUESTIONS? Send them my way at Christopher@spartansurfaces.com
EXPLORE ALL OUR FLOORING ANSWER ARTICLES
EXPLORE ALL OUR FLOORING ANSWER VIDEOS
ABOUT CHRISTOPHER
Christopher Capobianco covers the NY Metro and Connecticut area for Spartan. He’s a fourth-generation floor coverer whose family has been in the business since the 1930s. For 36 of the last 43 years, he’s had roles in retail, distributor, and manufacturer sales. The other seven years were spent in floor covering training and technical support. He also has been a part time columnist for various flooring magazines since 1988 and is a long-time member of the ASTM Committee on resilient flooring. You can reach him here.