Flooring Answers: Floating Floor Facts – Rigid Core LVP
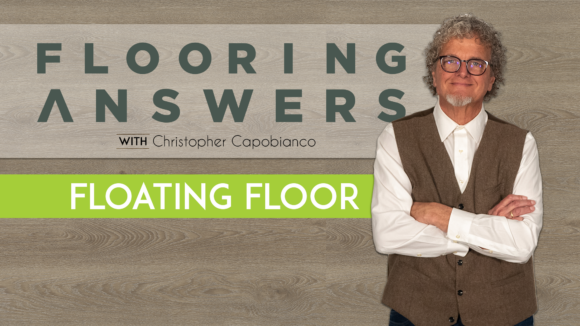
I first heard of floating floor when I was working for my family’s floor covering store in the 1980s. These first products were engineered wood floors from Europe. It sure was a foreign concept to us that you did not have to fasten it to the substrate. However, we were the kind of company that tried new products and materials readily, so we started to sell a little bit of it and found the installation to be as simple as advertised, as long as you follow some simple rules.
By the mid 1990s, laminate floors had arrived. Installed by the same type of system, they really took off, saving a great deal of time and substrate preparation compared to vinyl floors, which for 50 years prior, had been the number one choice for a lot of residential kitchens. A few years later, a big change happened with the advent of the “click” locking mechanism, which eliminated the need to glue the tongue and groove together. This made the installation of floating wood floors laminate floors even easier!
Fast forward to 2012 or so when an entirely new category of floating floors arrived with vinyl as the top layer, over a rigid polymer composite core and a “click” locking system very similar to laminate and wood floors. These floors are more water resistant, have a lower profile, have a slightly softer “feel“ and good acoustic performance for impact noise between floors of high-rise buildings. Now hugely popular for a lot of applications, especially residential apartments and hotel guest rooms, these products are identified with a variety of acronyms and terms such as LVP, LVT, WPC, SPC, Rigid core and “Waterproof” flooring, if not more.
However, we now have an industry standard, ASTM F3261 Standard Specification for Resilient Flooring in Modular Format with Rigid Polymeric Core* so for the purposes of this article and for most of my discussions in my day-to-day work, I use the term Rigid Core.
MIND THE GAP!
Even though floating floors of one kind or another have been sold in the United States since the 1980s, I am astonished how often some of the most important installation requirements are either ignored, or not even known in the first place. This is most egregious when it comes to allowing the floor to “float” by allowing expansion spaces. We usually don’t have anyone questioning recommendations for floating floors that have a wood or fiberboard core such as engineered wood, laminate, cork floating floors, and other wood-based core products. However, a lot of people seem to think that Rigid Core vinyl products do not require any expansion. This is not true!
Floating floor, including Rigid Core products, naturally expand and contract due to environmental changes, so specifications call for expansion gaps between the installed flooring and any fixed objects, and within the flooring itself on large jobs. Failure to allow the recommended gap forces the expansion away from the perimeter towards the center of the floor, creating pressure at the edges of the planks, causing them to lift, or “peak” like a tent. This can cause the locking mechanism to fail, and the peaked edges can be damaged by traffic.
To allow a floating floor to freely expand and contract naturally, do not install directly against any vertical objects. This includes walls, cabinets, fixtures, door jambs, pipes, steps, AND existing floor coverings such as tile, stone, wood, carpet or any other permanently installed floor. The “existing floor coverings” one gets ignored a lot because of the desire to have a flush installation of different types of floor coverings that meet each other. However, it is just as important as the expansion gap against the walls.
IT’S ALL IN THE DETAILS
The amount of expansion needed will vary from product to product, so check the manufacturer guidelines first. Here are some examples from one manufacturer, in italics: For areas up to 50’ in length, allow 1/4” expansion gap, and for areas 50’ to 80’ in length, allow 5/8”.
Also, in large rooms or a long run (such as a corridor), expansion gaps must be built into the floor covering itself. “For areas exceeding 80 feet in any direction, and/or areas exceeding 6400 square feet, a 5/8” expansion space must be allowed within the floor. To cover these spaces, use “T-moldings” or another suitable molding that covers the expansion space but allows the planks to expand and contract. I recently was involved in a major failure in the 110-foot-long corridor of an assisted living facility. The manufacturer required an expansion gap at 80 feet, but that did not happen so the planks “peaked” and locking mechanism failed in several places, causing gaps and breakage that had to be covered with duct tape until the floor could be replaced.
DON’T PINCH!
Expansion can also be hindered by heavy objects on top of the finished floor covering, or by fastening things to or through the floor covering. The weight of heavy cabinets, fixtures, reception desks, millwork, etc., prevents the floor from moving. Floating floors must always be installed after these objects are in place, allowing for the recommended expansion gap.
Moldings can also be a “pinpoint “. After installing, place moldings or wall base, attached to the wall (not the floor) and allow a slight clearance between the molding and the planks so that the moldings do not “pinch” the flooring. Again, the floor needs to be able to float.
TO GLUE OR NOT TO GLUE?
Most Rigid Core floating floor products are not supposed to be glued down at all, but manufacturers of some products may allow it in certain circumstances. However, doing a mix of glue down and floating within the same flooring area is a recipe for disaster. A recent claim I was involved with had a failure because the installers used adhesive on part of a hallway/lobby area. The rest of the floor was left floating, and this area was glued down. This led to uneven expansion, causing the planks to “peak.”
LET ME ROLL IT?
Another space where I advise caution on the use of floating floor is for areas that will be exposed to rolling traffic. That could be a high traffic retail or health care space, an office space with rolling desk chairs, or even a home where the resident may be in a wheelchair. Before using any type of a floating floor in these types of spaces, consult with the manufacturer of the flooring. Because of the potential stress on the locking mechanism caused by the rolling traffic, it may be recommended to choose a different type of floor covering that is fully adhered to the substrate.
FLATTER IS BETTER
The thicker construction and easier installation for rigid core products has created the impression that substrates for Rigid Core floors these floors need little or no compared to fully adhered resilient flooring. That is not true! The substrate still needs to be flat within the equivalent of 3/16” in10 feet, so sloping floors or substrates that have high or low spots need to be corrected prior to installing.
ACCLIMATION: THE FOUNDATION OF A BEAUTIFUL INSTALLATION
Although many Rigid Core manufacturers do not require acclimation of their products to job site conditions, that does not mean they can be installed in spaces that do not have environmental controls in place. In other words, the area wherethey will be installed needs to be fully enclosed with doors and windows and climate controlled 48 hours before, during and after installation. If you are involved in a project where the construction schedule has the floor going before doors, windows or HVAC systems, contact the flooring manufacturer for specifics on what they will or will not allow for their product.
With the huge variety of Rigid Core products being sold in our market today, coming from factories all over the world, understanding and following these requirements is very important.
*Referenced ASTM Standards available from ASTM International
(877-909-2786) or www.ASTM.org.)
About Christopher
Christopher Capobianco covers the NY Metro and Connecticut area for Spartan. He’s a fourth-generation floor coverer whose family has been in the business since the 1930s. For 36 of the last 43 years, he’s had roles in retail, distributor, and manufacturer sales. The other seven years were spent in floor covering training and technical support. He has been a part time columnist for various flooring magazines since 1988. He’s also a long-time member of the ASTM Committee on resilient flooring. You can reach him here.
EXPLORE ALL OUR FLOORING ANSWER ARTICLES
EXPLORE ALL OUR FLOORING ANSWER VIDEOS
About Spartan
Spartan Surfaces, a subsidiary of Floor & Decor, is a specialty flooring supplier headquartered in Bel Air, MD. Employing over 150 team members, Spartan holds warehousing and offices in Maryland and Minnesota with showrooms in D.C.and Chicago. Its geography encompasses eighty-five percent of the United States, with continued expansion on the horizon. Taking a human-centered approach, Spartan prides itself on great people dedicated to great products, great families, great friendships, and great happiness. Whatever you’re working on, we’ve got you covered!